More about transforming biomass
Most of the chemical products and energy we use everyday come from fossil fuel resources.
With an ever-growing global population, the demand for energy and chemicals is increasing rapidly. Given the negative environmental impact of our use of fossil fuels, it is vital that we find alternative resources.
Biomass is a sustainable alternative for fossil fuels. It can be obtained from natural sources as well as from various agricultural and industrial waste streams.1
Despite the complexity of the petrochemical industry, it is based on just a few key molecules serving as building blocks for an array of chemical products.
Similarly, a biomass-based industry is based on a small number of platform molecules including organic acids, sugars and alcohols.2
The challenge
These renewable platform chemicals are different to petroleum feeds for example, they contain more oxygen. Therefore, they require the development of different methods to achieve the same chemical products.
Modern industrial chemistry has been designed around petroleum-based feedstocks, so the processes and catalytic materials developed during the last few decades are selected to operate on hydrocarbons, with high thermal stability and under hydrophobic environments.
However, due to the nature of biomass-derived platform chemicals, processing at moderate temperature in aqueous solutions means that the catalysts employed must have different properties.2
Our research is developing these new catalysts.
1 S. Takkellapati et al, Clean Technologies and Environmental Policy (2018), 20, 1615-1630
2 J. C. Serrano-Ruiz et al, Chem. Soc. Rev. (2011), 40, 5266-5281
Here are just some of the familiar products we can make using biomass resources
...with a little help from catalysts
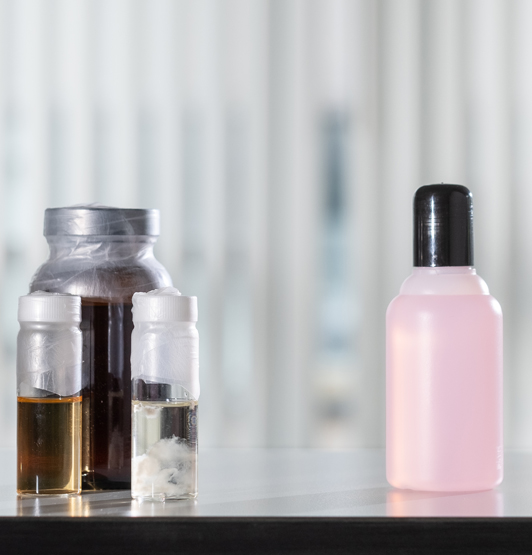
Fermentation broth to nail varnish remover
Acetone is a widely used industrial solvent, including in nail varnish remover. Currently, it is obtained from fossil fuels, as a by-product of phenol production.1 Attention has recently turned to the green production of acetone from renewable biomass resources which involves fermentation of sugars present in materials such as corn stover, wheat straw and switchgrass. The resulting fermentation broth contains acetone in very low concentrations along with two by-products, butanol and ethanol. If the acetone cannot be recovered in an energy efficient manner, then it will simply be lost as waste material. We can develop catalysts that selectively absorb acetone from these dilute mixtures and transform acetone into higher value chemicals.
1 F. E. Liew et al, Nature Biotechnology (2022), 40, 223-344
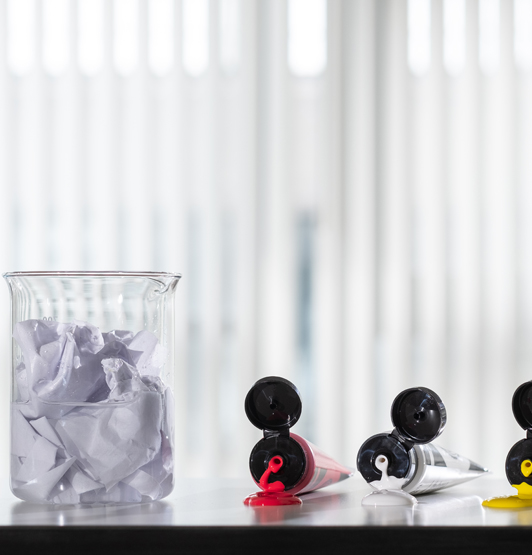
Paper sludge to acrylic paint
Paper recycling facilities generate wastewater containing a lot of paper sludge. It is high in polysaccharides – particularly cellulose – which can be broken down and fermented by bacteria to produce several products including lactic acid.1 Traditionally produced from fossil fuel, there is growing demand for lactic acid in many areas including food, pharmaceuticals and cosmetics. Obtaining lactic acid paper from sludge waste provides a green route to a number of chemical products while eliminating the issue of disposal. One of these products is acrylic acid – widely used in acrylic paints – which is created by dehydration of lactic acid with a catalyst.
1 S. Marques et al, Biochemical Engineering Journal (2008), 41, 210-216
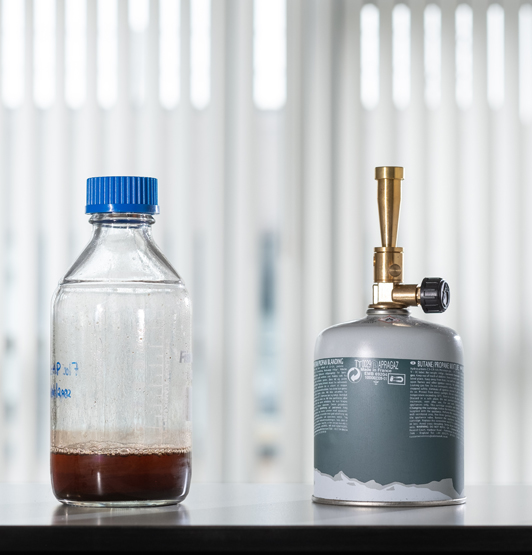
Refinery wastewater to combustible gas
There are many alternatives to crude oil including municipal solid waste, wood chips from wood mills and agricultural waste. Processing these materials creates a lot of wastewater due to the water content in the feedstock or the applied reaction conditions. The valorisation of the wastewater is essential for the economic feasibility of biofuel production. Aqueous phase reforming is a catalytic process which can be used to convert organic contaminants in the wastewater into a mixture of combustible gases. The utilisation of these gases increases the efficiency of a refinery by reducing waste production.
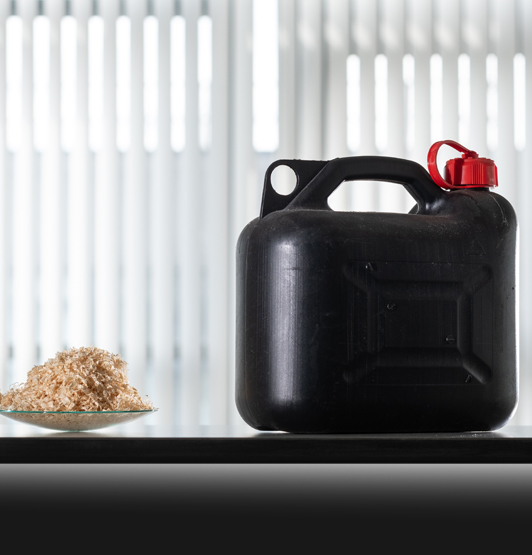
Woodchips to liquid fuels
Electric cars will play an important role in reducing our dependence on fossil fuels, but transport will continue to rely on energy-dense liquid fuels for the foreseeable future. There are many ways to produce synthetic oil – and wood is an excellent, readily available feedstock with high energy density. The biomass used for fuel production does not come from the deforestation of natural lands – it is waste from the furniture and paper industries or from timber plantations. Hydrothermal liquefaction or pyrolysis makes it possible to convert biomass into bio-oil which can then be converted into biofuels via several catalytic steps.
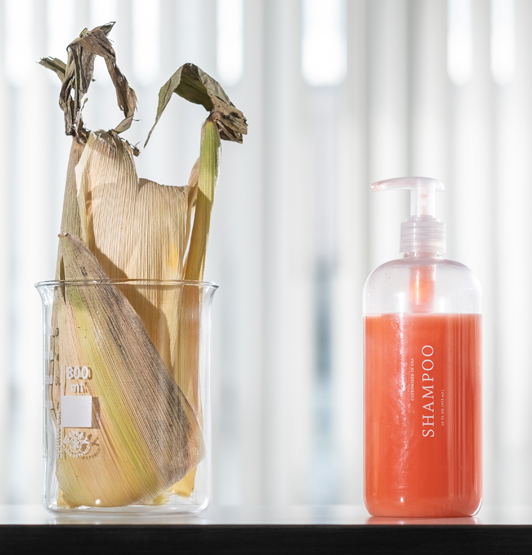
Corn husk to shampoo
Ethanol can be obtained by transforming biomass feedstocks – such as corn (maize) husk which contains a lot of cellulose – via biochemical or thermochemical pathways. The biochemical process involves the breakdown of cellulose into sugars which are fermented to ethanol. Meanwhile, the thermochemical process involves the treatment of feedstock with heat. The resulting mixture of CO and H2 gases produced is used for ethanol production by catalytic reaction. Both processes provide a green route for ethanol production. The Guerbet reaction is then conducted to synthesise n-butanol with the assistance of a catalyst. N-butanol can be used to make shampoo.
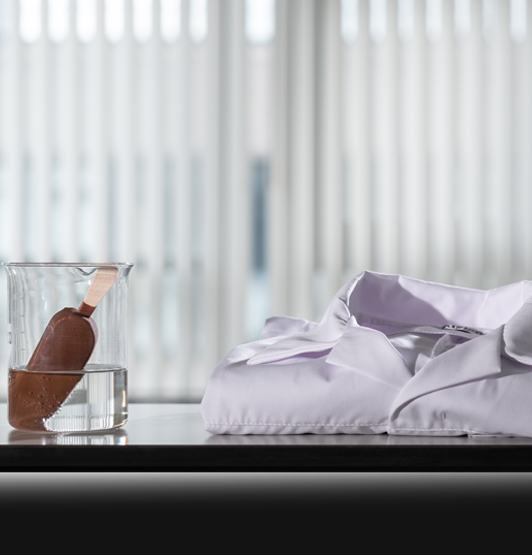
Ice-cream to bio-plastic fabrics
5-(hydroxymethyl)furfural (HMF) is produced from the dehydration of biomass-derived carbohydrates which are present in wastewater streams from food manufacturing sites such as ice-cream factories. HMF can be converted into 2,5-furandicarboxylic acid (FDCA) which has the potential to replace terephthalic acid - used in the production of polyethylene terephthalate (PET). PET is a thermoplastic polymer resin used in fibres for clothing.
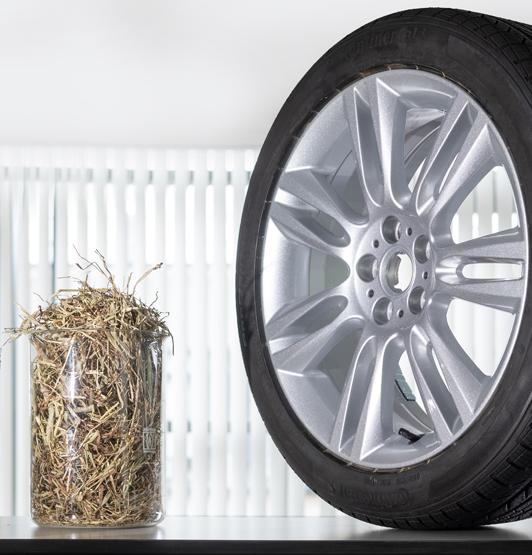
Straw to car tyre
Butadiene is one of the most widely used raw materials in the production of synthetic rubber. Normally, it is obtained directly by “cracking” petroleum. Recently, butadiene has been obtained by fermenting straw, beet, corn and woodchips. This process has been demonstrated by Michelin’s Bio Butterfly project. In this procedure, “ethanol is partially transformed into butadiene” by reacting “in the presence of a catalyst and under specific pressure and temperature conditions”. This process requires distillation and purification to get to the final “bio-sourced butadiene”. Michelin claims “it will integrate an average of 40% sustainable materials in its tyres” by 2030, reaching 100% by 2050.1,2
1 Michelin - "Bio-Sourced Materials: A New Milestone" (Accessed May 2022)
2 Michelin - Media Day Michelin 2021 (Accessed May 2022)
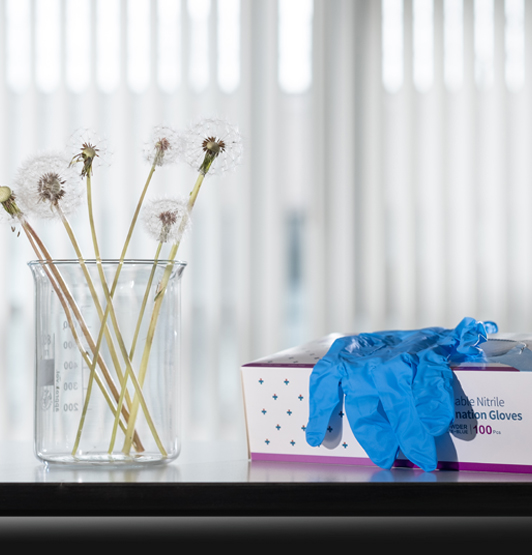
Dandelions to latex gloves
Dandelions are among the most reviled garden weeds – but could provide us with an awful lot of rubber. Caoutchouch – the raw material for rubber production – is found in the milky sap of different types of dandelions, including Taraxacum kok-saghyz (TKS) known for its high latex content. TKS was first considered as a source of rubber during World War II when natural tree rubber became too expensive. Attention has once again turned to the dandelion, and researchers are investigating how to improve yield per plant to ensure scalability and enhance commercial viability across a range of products spanning tyres, mattresses, gloves, tape and technical rubber articles.1, 2
1 "Continental honored by University of Münster for research on dandelion tires" (Accessed May 2022)
2 "Green tyres: alternatives to petrochemical rubber" (Accessed May 2022)
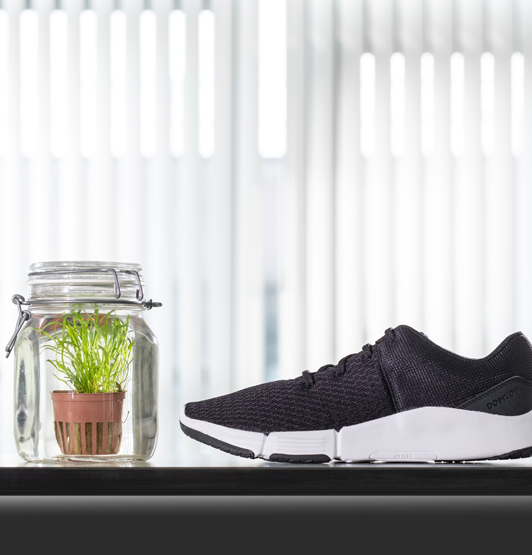
Algae to trainers
Pollution and rising temperatures in our rivers and lakes encourage the growth of algae – harming animals and plants. By harvesting algae, we can create eco-friendly, bio-sourced materials for our shoes. Drying the algae, crushing it into a powder and mixing it with ethylene-vinyl acetate creates an algae foam that can be press-moulded into outer and inner soles. This would cut the synthetic materials used in shoes by up to 20% – while controlling algae populations, improving water health and reducing CO2 emissions.