Additive manufacturing enhances the performance of functional ceramics
Professor Bala Vaidhyanathan - Aeronautical, Automotive, Chemical and Materials Engineering
High Value Manufacturing
Ground-breaking work, pushing the boundaries of the additive manufacturing (AM) of ceramics, has created a working prototype that surpasses existing positive temperature coefficient resistor (PTCR) heaters for a number of applications.
PTCR ceramics appear in household items including hairdryers and hobs, but they are also widely used in the automotive and aerospace sectors where component weight can be of critical importance – not least in combating carbon emissions.
Their honeycomb structure is conventionally manufactured using injection moulding or by drilling solid ceramic components. The research has demonstrated that using AM technologies reduces materials waste and provides an efficient manufacturing process with significant design freedom.
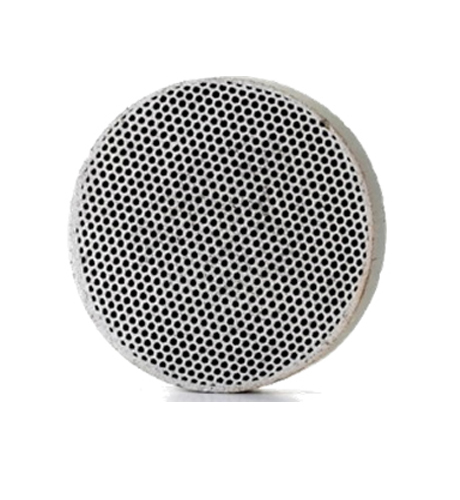
The work involved the development of novel aqueous, eco-friendly ink formulations with suitable rheological properties. These were used to create 3D printed components of varying sizes and shapes as well as prototype high-density honeycomb lattices.
The sintered densities of the 3D printed components are >99% of the theoretical density for this material, and they are almost 50% lighter than those manufactured traditionally. What’s more, they have excellent heating properties.
Work is ongoing to refine this sustainable manufacturing process and further enhance component performance.