Research
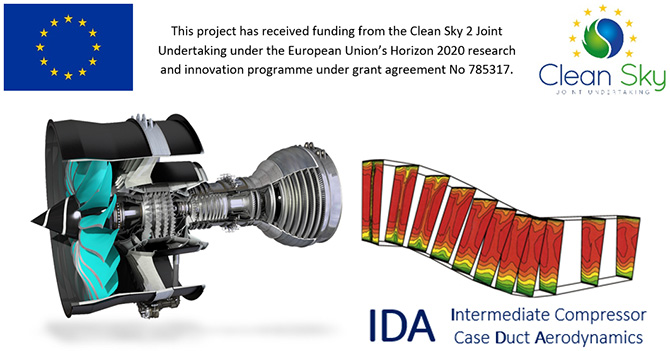
IDA Project
Principle Investigator: Dr A Duncan Walker (a.d.walker@lboro.ac.uk)
IDA was a 2-year, €500k collaborative project funded from by Clean Sky 2 under the European Union’s Horizon 2020 research and innovation programme. It comprises of a partnership between the Universities of Loughborough and Chalmers with GKN Aerospace.
The key objective of the project was to help reduce air-traffic emissions by improving the thermal efficiency of aero-engines. To reduce fuel burn and CO2 emissions there is a drive towards very-high bypass ratio geared turbo fans with small ultra-high-pressure ratio core engine technologies. Although this increases propulsive and thermal efficiency it makes the design of the ducts connecting the various compressor spools much more challenging as the change in radius becomes much greater. IDA has developed more integrated duct technologies that will contribute to the development of a very-high bypass ratio turbo fan demonstrator (e.g., UltraFan™). Loughborough University provided experimental validation of an initial GKN Aerospace duct design using a fully annular, low-speed test facility incorporating a representative compressor stage. Chalmers University used these data to establish and validate best practice for advanced, yet efficient, CFD methods (e.g., hybrid RANS/LES). Together, the three-way collaboration then developed an improved design solution offering higher efficiency, lower impact on system performance and improved stall margin. This was subsequently validated on the low-speed test facility thereby delivering future potential duct technologies for the UltraFan™ engine and other very high bypass ratio applications.
Background
Key technologies must be developed to achieve the environmental and economic targets set out by ACARE Flightpath 2050 - Europe's Vision for Aviation. These ambitious targets aim to reduce, by 2050:
- CO2 emissions by 75%
- NOx emissions by 90%
- Perceived aircraft noise by 65%
(compared to technology levels in 2000).
Innovative, very-high bypass ratios and smaller ultra-high-pressure ratio core engine technologies will be required in order to increase the propulsive and thermal efficiency of engine cycles and thereby reduce fuel-burn and CO2 emissions. To maximise the efficiency of modern turbofan engines the compression system is generally split into two or three parts. These low, intermediate and high-pressure compressors are mounted on separate shafts (or spools) allowing each to rotate at an optimum speed and hence deliver an optimal work balance. To maximise the performance of this multi-spool design, the diameter of each spool must reduce as the air density increases through the compression system. To accommodate this, annular S-shape ducts are employed to connect the upstream and downstream spools. Within such ducts flow separation must be avoided if, in line with overall cycle performance, the stagnation pressure loss is to be minimised and the downstream compressor performance not adversely affected. However, what appears to be a relatively simple geometric shape poses some significant aerodynamic challenges because of the complex nature of the flow field which develops under the combined influence of pressure gradients and streamline curvature effects. As the flow follows a curved path through the duct a modification to the static pressure field occurs. Across the first bend a radial pressure gradient is required to turn the flow inwards towards the engine centreline, so that the pressure close to the outer casing is higher than that adjacent to the inner. Within the second bend the flow is returned to the axial direction and so this radial pressure gradient is reversed. As a consequence, stream wise pressure gradients are generated that influence the flow field development in various regions of the duct, including the boundary layers that develop along the duct walls. For a compressor transition duct, this means that the axial loading is highest, and hence the flow most likely to separate, along the inner wall on the second bend. The ability to design shorter, aggressive compressor transition ducts is advantageous from a performance and weight saving perspective. However, increases in bypass ratio, the potential inclusion of geared fan architectures and decreases in the relative size of ultra-high-pressure cores means that the change in radius between compressor spools will increase. Hence, the design of increasingly aggressive transition ducts is therefore imperative for the development of future low emission aero gas turbines.
The aerodynamic design of compressor transition ducts is further complicated by the fact they must provide stable performance over a range of operating conditions. This includes incorporating a bleed flow to extract ice particles or ingested water. This bleed is usually placed immediately upstream of the transition duct. However, little attention has been given to understanding how this integrates aerodynamically with the upstream compressor or the duct. Furthermore, transition ducts are subject to strict structural requirements as they provide radial stiffness and load paths to the engine mounts and for bearing support. To facilitate this, radial struts with an aerodynamic shape are placed in the main gas path and these also serve as passages other secondary services. It is crucial that these mechanical requirements are integrated into the aerodynamic design without penalty.
IDA Technical Objectives
- To perform an experimental validation, at low TRL, of the aerodynamic design of the IP-HP compressor inter duct for the large turbo fan demonstrator (UltraFan™). The tests will be conducted on a fully annular isothermal test facility will incorporating a representative upstream compressor stage and inter duct. Aerodynamic data will be recovered by preforming area traverses through the compressor and duct using a combination of five-hole probes and hot-wires. After the initially tests without bleed but then a representative bleed port will be added upstream of the duct, on the outer casing, and the compressor/bleed/duct interaction studied.
- To develop, demonstrate and experimentally validate potential future technologies for inter ducts for future UltraFan™ and very high bypass ratio applications. Tests will incorporate a second design solution optimized for a more effective bleed extraction and/or lower impact on system performance and stall margin.
- To establish an advanced, yet efficient CFD approach (e.g. hybrid RANS/LES) to predict the flow in advanced compressor inter ducts. The experimental data generated within the project will be used to validate best practice methodologies which will provide increased numerical accuracy but with a reasonable turn-over time and robust performance.
- Improved understanding from the initial experiments and CFD will be used to develop a further design solution optimised for a more effective bleed extraction and/or lower impact on system performance and stall margin. This will then be experimentally validated on the low-speed test facility thereby delivering future potential duct technologies for the UltraFan™ engine and other very high bypass ratio applications.
IDA Results and Publications
The key results and impact of the IDA project are:
- 1. Technology validation of transition duct prior to engine demonstrator programme
IDA has experimentally validated, at TRL 3-4, the aerodynamic design of the IP-HP compressor inter duct for the large turbo fan demonstrator (UltraFan™). Importantly this incorporates a new, untested bleed. Hence the IDA has enabled the design to be taken forward to the higher TRL, higher cost. engine demonstrator with reduced risk.
- 2. Technology validation for advanced, integrated compressor duct design for future geared turbofans
Improved understanding has been exploited to develop a new design solution with better integration of the main gas path with secondary systems. This has been experimentally validation within IDA to TRL 3-4 and will pave the way for future duct technologies application to the UltraFan™ engine or other very high bypass ratio applications.
- 3. Advanced CFD tool and guidelines
Through better understanding of the fundamental flow physics IDA has delivered a validated advanced, yet efficient CFD approach to predict the flow in advanced compressor inter ducts with increased numerical accuracy but with a reasonable turn-over time and robust performance. This will be exploited by both academic and industrial stakeholder in the design of future transition ducts for future low emission engine architectures.
Publications:
- Spanelis, A., and Walker, A. D., “Aerodynamic Influence of a Bleed on the Last Stage of a Low-Pressure Compressor and S-Duct”, ASME. J. Turbomach. February 2022; 144(2): 021007. https://doi.org/10.1115/1.4052134
Other planned publications:
- “Experimental Investigation of the effect of a Bleed on the Last Stage of a Low-Pressure Compressor and S-Duct”, in preparation for ASME Turbo Expo 2022.
- “Advanced Integrated Bleed for Compressor Transition Ducts”.
- “Advanced CFD Techniques for the Investigation of Compressor Transition Ducts”.
Selected other relevant publications:
- Walker, A.D., Barker, A.G., Carrotte, J.F., Bolger, J.J., and Green, M.J., 2013, “Integrated OGV Design for an Aggressive S-shaped Compressor Transition Duct”, ASME. J. Turbomach., 135(1).
- Walker, A.D., Barker, A.G., and Carrotte, J.F., 2011, “Numerical Design and Experimental Evaluation of an Aggressive S-shaped Compressor Transition Duct with Bleed”, ASME Paper No. GT2011-45628.
- Walker, A. D., Barker, A. G., Mariah, I, Peacock, G. L., Carrotte, J. F., and Northall, R. M., 2014, “An Aggressive S-Shaped Compressor Transition Duct with Swirling Flow and Aerodynamic Lifting Struts”, ASME Paper No. GT2014-25844.
- Wallin, F., Bergstedt, R., Peacock, G. L., and Walker A. D., 2015, “Aerodesign and Validation of Turning Struts for an Intermediate Compressor Duct”, 22nd ISABE Paper No. 2015-22143.
- Siggeirsson, EMV, Andersson, N, and Wallin, F., 2018, “Numerical and Experimental Study on Bleed Impact on Intermediate Compressor Duct Performance”, ASME Paper No. GT2018-76649.
- Walker, A. D., Mariah, I., Tsakmakidou, D., Vadhvana, H., and Hall, C., 2020, “The Influence of Fan Root Flow on the Aerodynamic of a Low-Pressure Compressor Transition Duct", ASME. J. Turbomach., 142(1).
- Walker, A. D., Mariah, I., and Hall, C., 2021, "An Experimental, Aerodynamic Evaluation of Design Choices for a Low-Pressure Compressor Transition Duct", ASME. J. Turbomach., 143(9).
- Siggeirsson, E. M. V., Andersson, N., and Burak Olander, M.,2021 “Numerical and Experimental Aerodynamic Investigation of an S-Shaped Intermediate Compressor Duct with Bleed”, ASME. J. Turbomach., 143(10).
- Tsakmakidou, D., Mariah, I., Walker, A.D., Hall, C., and Simpson, H., 2021, "Experimental Investigation of Secondary Flows and Length Reduction for a Low-Pressure Compressor Transition Duct", ASME J. Gas Turb. And Power, doi.org/10.1115/1.4052086.
IDA Partners
Loughborough University - UK
Dr A Duncan Walker, the IDA Project Coordinator, is a Reader in Applied Aerodynamics at Loughborough University and a member of the academic management team for the University Technology Centre (UTC) in Combustion System Aerothermal Processes. He has 20 years of research experience the experimental and computational study of the internal flows within modern gas turbines. Fundamentally this includes diffusing flows, boundary layer separation, wake mixing, secondary flows, and the effects of swirl, curvature and pressure gradients. This extends to more applied systems such as low emission combustor architectures, the compressor/combustor interface, integrated outlet guide vane design, advanced pre-diffuser development, fuel injector design, the combustor/turbine interface and transition duct aerodynamics. He has been directly involved with compressor duct research since the early 2000’s and has worked on several large collaborate programmes as either a CoI or PI (EU – AIDA, LEMCOTEC, NEWAC and Innovate UK – iCORE).
Chalmers University of Technology - Gothenburg, Sweden
Dr Niklas Andersson is an associate professor at Chalmers and a specialist in computational aero-acoustics and compressible fluid flow. Niklas also has extensive industrial aerospace experience in the field of computational fluid dynamics analysis and the development of computational software. Niklas has been involved in several EU-programs (JEAN, CoJeN, HiSAC, FLOCON, ULTIMATE, TurboNoiseBB) where detailed flow simulation and acoustics have been the central elements.
Chalmers Tekniska Hoegskola was founded in 1829 and is an independent foundation since 1994. Chalmers acquires around 70% of its research funding from external sources. More than 14 000 people, including over 12 000 undergraduates, work and study in some of Chalmers’ 17 departments. The research group turbomachinery and aero-acoustics, consisting of two professors, two senior researchers and 11 Ph.D. students, is part of the Fluid Dynamics Division at the Department of Mechanics and Maritime Sciences. The research group has an extensive experience in contributing to research efforts in European programmes such as: JEAN, CoJeN, HISAC, AIDA, AITEB2, VITAL, NEWAC, DREAM, FLOCON, E-BREAK, LEMCOTEC and ENOVAL. The primary research focus of the turbomachinery and aero-acoustics group is jet engine system analysis and engine concept evaluation as well as detailed flow and acoustics analysis for specific sub-problems such as compressors, turbines, transition ducts, intercoolers, combustors/afterburners and nozzles.
Funding
This project has received funding from the Clean Sky 2 Joint Undertaking under the European Union’s Horizon 2020 research and innovation programme under grant agreement No 785317.