Adiabatic compressed air energy storage (ACAES)
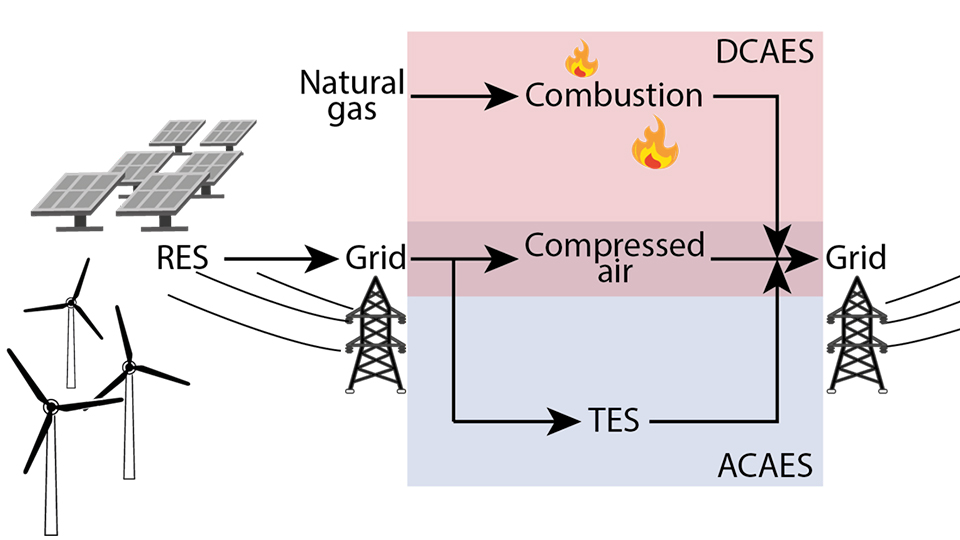
Energy storage is needed to build low-carbon economies and Adiabatic Compressed Air Energy Storage (ACAES) is a novel concept for energy storage which has the potential for widespread, large-scale, low-cost implementation.
Our aim
The concept of ACAES is well-established but there are a range of engineering challenges which are yet to be overcome for the technology to be adopted. One significant problem with current design of ACAES systems is the transient storage pressures which cause inefficient turbomachinery operation and introduce losses. Our research seeks to address these challenges by developing a novel method of isobaric air storage.
Our research
The principle of ACAES is as follows; to charge the system electricity is used to drive compressors which generate hot compressed air. Since storing hot air is volumetrically inefficient, the excess thermal energy must first be removed from the hot air and stored in a separate thermal storage medium. The cool compressed air is then separately stored in a High-Pressure (HP) air storage vessel. This HP vessel can either be an artificial container or a naturally occurring cavern. Thermodynamically speaking, the charging process corresponds to converting electrical energy from the grid to shaft rotational kinetic in the electric motors driving the compressors, which in turn, converts it to physical exergy in the air. This is split into two sub-components: the exergy associated with the elevated pressure of the air mass within the HP air store and the thermal exergy contained in the thermal energy storage.
ACAES is distinct from diabatic Compressed Air Energy Storage (CAES), where instead of thermal storage heat is provided by the combustion of fossil fuels. Two diabatic CAES plants have operated for over 30 years (Huntorf CAES, Germany, and MacIntosh CAES, USA). These two system types are illustrated below. See figure above illustrating the difference between ACAES and diabatic CAES. Diabatic CAES uses fossil fuel combustion whereas ACAES replaces this with a thermal energy storage (TES) unit.
In this project we are exploiting the high compressibility of CO2 in the two-phase liquid-vapour region to create a ‘pressure buffer’, allowing the pressure change during charge and discharge to be minimised, thus improving performance. We are also interested in other methods of isobaric storage, including hydraulic compensation and flexible boundaries.
Our outcomes
We are developing detailed thermodynamic modelling of typical system designs to understand where the disparities between theoretical predictions of performance and realised experimental performance arise. Our work suggests that the heat exchanger in ACAES systems is a major difficulty – since there is a natural effectiveness-reversibility trade-off (i.e. the more effective the Heat Exchanger (HX) operation – the harder it is to keep the operation close to reversible). Therefore, we are exploring new heat exchanger designs for this application.
Innovative energy storage solutions will be required to integrate vast amounts of renewable energy generation in future. ACAES has the potential to provide a low-cost large-scale solution for the energy storage needs of a sustainable, low-carbon economy.