Research
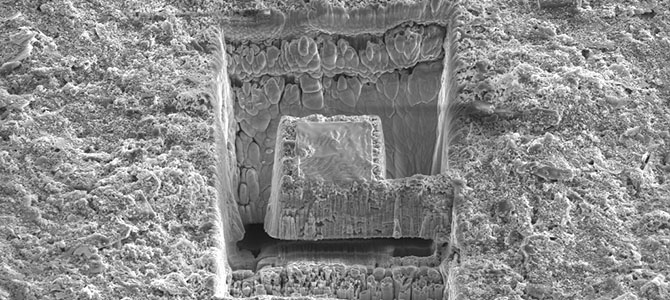
Technique Development
All areas of Materials research have benefited from advances in techniques to explore and explain the structures and interactions taking place at a molecular and atomistic level.
Two of the key enabling areas of technique research that cross-cut with our other areas are Materials Modelling and Characterisation techniques.
Modelling research in the Department encompasses a broad range of techniques. By using them to understand the structure and properties of materials at the atomic scale, we are able to understand how the macroscopic behaviour of the materials depends on composition and processing, and optimise materials for new applications.
Staff within the Loughborough Materials Characterisation Centre not only make use of state of the art instrumentation but work with researchers and instrument manufacturers to develop new techniques, particularly in the areas of three dimensional microstructural characterisation and in-situ testing.
Activities we address include but are not limited to:
- Materials Modelling
- Understanding microstructural evolution, particularly to predict life expectancy of high-temperature materials in service
- Predict the growth of thin film materials under different growth conditions
- Understand what factors control the degradation of bioactive glasses implanted into the body
- Model the damage mechanisms and the evolution of damage in materials for use in nuclear power production
- Materials Characterisation
- Three dimensional microstructural characterisation.
- In-situ heating to replicate in service conditions of materials.
- Micro mechanical testing to provide input data and validation of mathematical models.
More about us
Phosphate glasses for biomedical applications
Phosphate glasses dissolve harmlessly when implanted into the body, at a rate which depends very sensitively on the composition of the glass. This makes them applicable as delivery devices for drugs, nutrients, or antimicrobials, where these need to be delivered at a controlled rate. Over the past few years, we have used computer simulation to understand the structural features of the glass which control the dissolutions, and the effects on the dissolution of including therapeutically useful molecules.
Read more about this case study »
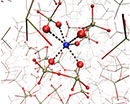
TEM In-situ heating to replicate service conditions
An investigation to examine the effectiveness of new technology to allow the in-situ heating of samples within the closed environment of a TEM. The in-situ investigation for bulk materials was enabled by focussed ion beam sample preparation. Site specific TEM samples are produced and transferred onto a heating chip using our in-house FEI Nanolab FIB. The chip allows for heating up to 1300°C with heating and quenching rate 200°C/millisecond.
The microstructure of the material can be studied in real time as it is being heated or cooled, even thermal cycles can be simulated at a fast rate. This new development allows us to study dislocations and precipitation/dissolution of second phases as a function of temperature to name a couple of examples.
Read more about this case study »
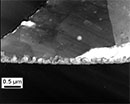
In-situ micro bend testing of SiC and the effects of Ga+ ion damage
Abstract:
The Young's modulus of 6H single crystal silicon carbide (SiC) was tested with micro cantilevers that had a range of cross-sectional dimensions with surfaces cleaned under different accelerating voltages of Ga+ beam. A clear size effect is seen with Young's modulus decreasing as the cross-sectional area reduces. One of the possible reasons for such size effect is the Ga+ induced damage on all surfaces of the cantilever. Transmission electron microscopy (TEM) was used to analyse the degree of damage, and the measurements of damage is compared to predictions by SRIM irradiation simulation
Read more about this case study »
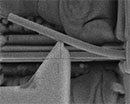
Academics involved with Materials Modelling technique development:
The team involved with Characterisation technique development:
- Patricia Cropper
- Scott Doak
- Shaun Fowler
- David Grandy
- Luke Jones
- Ryan MacLachlan
- Sabrina Yan
- Keith Yendall
- Zhaoxia Zhou